Laser Alignment
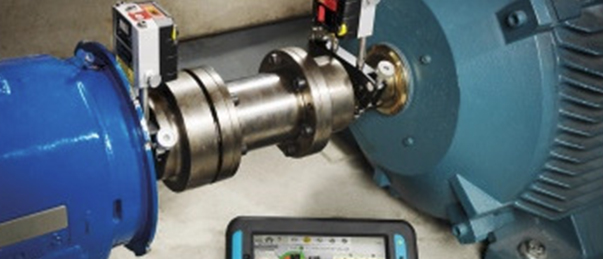
Shaft alignment
Is the process of aligning two or more shafts with each other to within a tolerated margin. It is an absolute requirement for machinery before the machinery is put in service.
When a driver like an electric motor or a turbine is coupled to a pump, generator, or any other piece of equipment, it is essential that the shafts of the two pieces are aligned. Any misalignment between the two increases the stress on the shafts and will almost certainly result in excessive wear and premature breakdown of the equipment. This can be very costly. When the equipment is down, production might be down. Also, bearings or mechanical seals may be damaged and need to be replaced. Flexible couplings are designed to allow a driver (electric motor, engine, turbine, hydraulic motor) to be connected to the driven equipment. Flexible couplings use an elastomeric insert to allow a slight degree of misalignment. Flexible couplings can also use shim packs. These couplings are called disc couplings. Tools used to achieve alignment may be mechanical or optical, as the Laser shaft alignment method or they are gyroscope based. The gyroscope-based systems can be operated very time efficient and can also be even used if the shafts have a large distance (e.g. on marine vessels).
Misaligned rotating machinery causes the high cost to the industry as it causes premature damages to the machinery, loss in production and excessive energy consumption. Misalignment is the most common cause of machinery malfunction. A poorly aligned machine could cost 20% to 30% of machine downtime, replacement parts, inventory and energy costs. Large returns are usually seen by regularly aligning the machine. The total operation life is extended and process conditions are optimized for efficiency. Hence it becomes extremely important for the maintenance and engineering professionals to understand machine malfunctions caused by misalignment.
Only 7% of measured machines within acceptable tolerances
A survey conducted by one of the world’s leading rotating equipment service organizations shows that less than 10% of the 160 machines randomly chosen for measurement were found to be aligned within acceptable limits. Under which category do your machines fall?
Are your machines aligned within the specified tolerances?
The effect of increased coupling loading due to misalignment can readily be shown using infrared thermography. Not only does the flexible element coupling heat up, but the machines also develop elevated temperatures, particularly around the bearing housings.
RATHIPOLYBOND as leading manufacturer and supplier of Flexible couplings understand the importance of Alignment of shafts. We have a team of specialist who can visit and study various alignment issues at your site. RATHIPOLYBOND can carry out Laser Alignment and save $$$ in your annual maintenance budget.
ADVATAGES OF LASER ALIGNMENT :
Laser alignment can be ten times faster and 100 percent more accurate compared to dial gauges or straight edge methods (depending on the user’s skill). The average dial setup will not measure down to 0.001 mm – but a laser can. A laser alignment system is quick to set up, easy to use and much more reliable than old technology. The latter often requires extensive experience and sometimes complicated calculations to be used. For example fixtures for dial gauges always drop a little, which affects the accuracy of the gauge’s displayed value. This is not the case with laser alignment. With a laser alignment system, it is possible to generate PDF reports directly from the instrument. The computer handles a number of targets and tolerances and it is easy to interpret the results. The possibility of documenting the results gives better control over the machines and greater assurance. Reports can be generated for “before” and “after” alignment. A laser alignment tool allows you to easily detect possible soft foot and weak foundations, which may cause the machine to get damaged due to vibrations. Laser alignment tools make the process of measurement and correction much more disciplined and repeatable. Rulers and dial gauges are not sufficiently accurate for today’s modern machines. Using laser alignment always gives the same results regardless of who takes the measurements. With laser alignment, you eliminate errors associated with old technologies such as bar sag, substandard dial bar, and mistakes when setting up the clamps.
For more details please contact RATHIPOLYBOND condition monitoring team and we will arrange the visit of our specialist to your place.